I are geophysicist. I were teached counting good, honest!
Anyway,
Before, the jacks in the castle were insisting on sitting at a 30 degree angle, and (oddly enough) nothing I did could fix that. Because of course, the shafts were unbalanced.
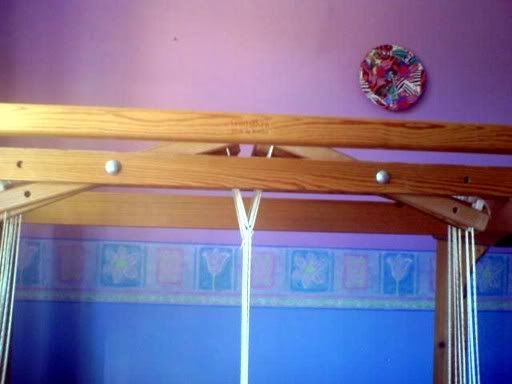
After, the jacks are now so even you can't even see them in the castle from this angle:
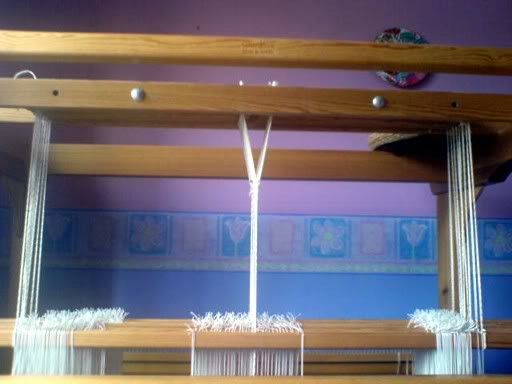
And so, with that, I could finish tying up this project and finally make a start on weaving. There's nothing quite so tempting as a fresh warp on a loom, just inviting you to weave it.
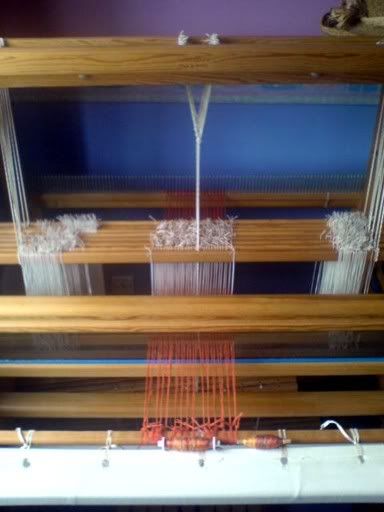
Only in this case, there was still quite a bit of twisting in the tail of the warp to be evened out before any decent weaving could be done. That's where the leader comes in. I always weave a piece of scrap cotton (or other yarn of a similar diameter to that of the weft) for an inch or so before I start weaving with the actual weft. This evens out the warp spacing and also allows you to find any warping errors that may have eluded you until now. Then I weave an inch or so with the weft I plan to use and when that's in place, I hemstitch the bottom few picks. That will keep the weaving in place once it's off the loom. When I'm done weaving and remove the fabric from the loom, I then simply unweave the leader from the fringe and the piece is ready to be finished. You can see the leader in purplish cotton at the base of the weaving here:
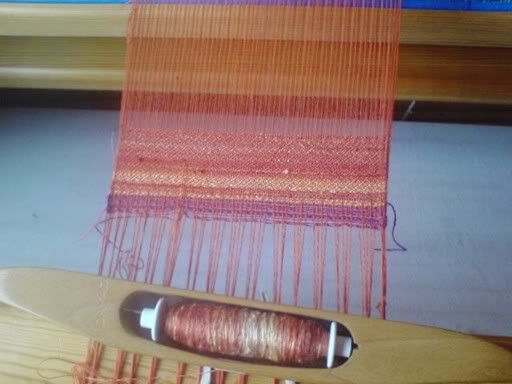
After all of the pain of getting the cashmere onto the loom, it was really quite well behaved once I'd started weaving. I'm weaving this at a quite loose tension to reduce the pull on the delicate warp threads, and I'm advancing the fabric much more rapidly than I normally would: I'm pulling the fabric forward after I've woven every inch or so.I'v woven somewhere from 4-6 inches and so far I've been rewarded with no further brekages, which has pleased me greatly.
I've chosen this weave structure to compliment the colours. Because the silk is yellow, orange, red and brown going through the brick-red cashmere, I wanted a weave structure that would reflect flames licking softly:
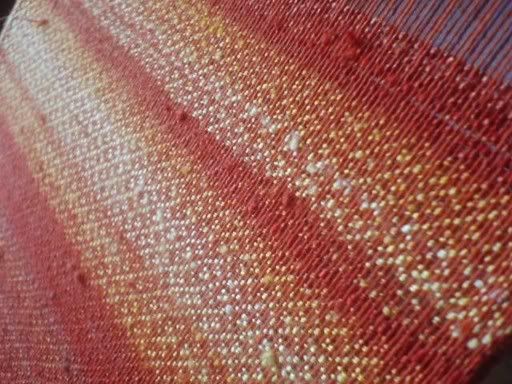
I think I've achieved that. And as this weave is based on an advancing twill, it ought to have a lovely drape as well.
And I've come up with a colour match for the next scarf as well. The next one is going to have a handspun silk cap weft in three different shades of brown with yellow accents. I had thought it was going to have a brown or caramel warp, but it appears to be screaming to be matched with yellow 60/2 silk....
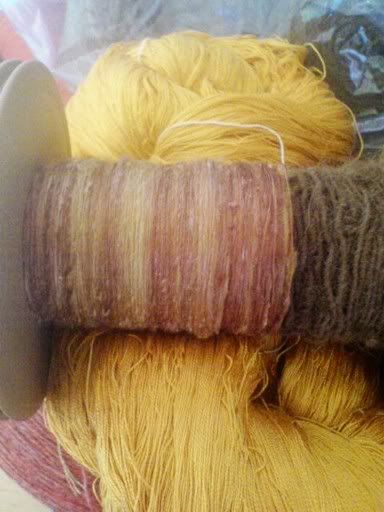
Don't you think?